Imagine a set of carbon wheels that claims to have 40% better impact strength, be 40% stiffer laterally, and about 20% lighter with a rider weight limit that’s about 30% higher than normal. Think that wheelset would weigh in at 1,035g? That’s what Filament Spin Evolution has done with their 25mm deep tubulars thanks to a non-standard construction method.
FSE isn’t the first brand to do filament wound carbon rim construction, that honor goes to Venn Composites and their REV wheels. FSE’s process brings the process in house using the same process used to create F1 driveshafts and by BMW. It was originally developed by DuPont decades ago, but hasn’t seen widespread use other than limited use by Wound Up forks and tubes for Calfee and a couple other small builders. Dan Kellerbee, FSE’s managing partner, says the process loves the cylindrical shape, which is why it worked so well for those products. They were already making rims for other brands using the traditional cut and layup process, but for their own brand they found a way to do filament spinning on the rim shape…
The filament winding process is wound around a mandrel to create the fairing (body) for the rim. Then, the bed of the rim (where the tube sits) is also mostly wound, more so on the tubular than the clincher, with a little bit of molding and machining required to get the hook for clinchers.
Those strength and stiffness claims come from testing these FSE rims compared to the standard rims they were making for other brands. They’ve done those tests in house, but they’re working on getting third party, independent tests done soon. The weight savings come from reduced resin needs and reduced carbon since they don’t need nearly as much overlap as you do with traditional sheets of carbon fiber being wrapped around a mold. There’s also no air bubbles because excess resin is essentially wiped from the filament before its wound into the thread that creates the fibers…and that excess is recaptured, too, so it’s not wasted. All told, it results in a rim with thinner walls but is stronger.
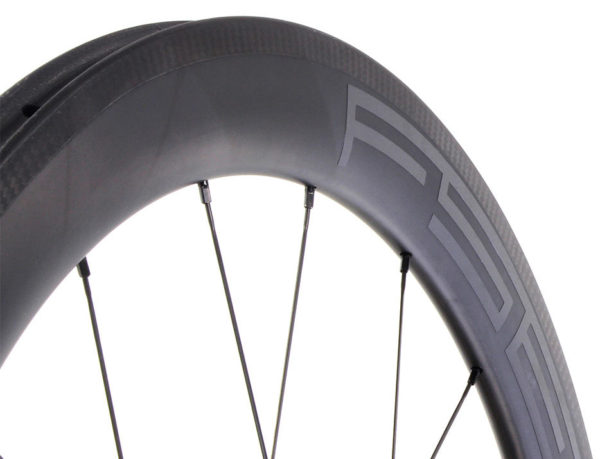
The rims come in UD and 3K finishes, which is a cosmetic layer added at the very end of the filament wind.
It’s not just their rims they’re excited about. They’re premium private label hubs made with stainless steel bearings paired with a set of three three-notched pawls and 48-tooth ratchet ring for quick, solid engagement. By the end of 2016, they’ll also offer them with White Industries hubs as an upgrade option.
Rim depths come in 25mm, 35,mm, 45mm, 55mm, 69mm and 79mm depths. All are 26.65mm wide for both clincher and tubular, with the clincher’s internal width being about 17.9mm. The clinchers can be set up tubeless with the Effeto Mariposa tubeless conversion kit. Prices range from $1,549 to $2,500, with Extralite rims pushing that top end pricing. Rims are $600 each on their own, with weights starting at 280g (25mm tubular) and go up to 590g (79mm clincher). The clincher adds about 80g over the tubular weights.